

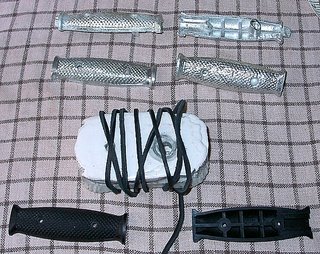

The first part of making a handle out of metal is to make the mould. I used a two part material called ATV325. It mixes like epoxy, and forms a rubber like compound which surprisingly enough, is quite resistant to heat. Useful since I would be pouring molten pewter into it! I used the existing handle halves to form the mould. Those are the black handle halves you see in the above pictures. Unfortunately, I didn't know how "rubbery" it really was, and its jello like consistency caused some problems due to distorted moulds. Well, that is the learning process I guess! I tried a couple of ways to pour....through the side, through the top. The top picture is of the mould wrapped up with a leather thong ready to use, with some of the cute little handle halves I made. I eventually made about 12 of them, of which 3 were good enough castings to actually use, and another six which simply got tossed back into the frying pan to melt.
There are things about pewter I never realized. For one thing, there is the "fizz" which comes out of it when it is poured. Like bubbles in soda pop, they seem to come from nowhere, and the bubbles come up the "sprues", making the sprues really porous. Ruins the surface of the casting as well...you can see how rough it makes the casting in some of the pictures above.
The end result of a couple of days trial and error (its not like I ever did anything like this before!) I got a nice bunch of nice hard shiney pewter handles, covered in pits from bubbles, oxodized from overheating, several little blisters on my hands, and a warm feeling. No wait, that was from the hot plate I forgot to turn off!
Click on images to enlarge.
2 comments:
I continue to be amazed at your craftsmanship.
And I, by your kindness.
Post a Comment