

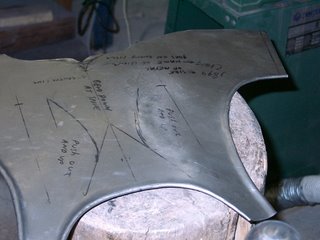
Bouging is one of those terms which means pretty much what you think it means. You place the steel sheet over a divot in the wood and bouge it with as big a hammer as you can swing with one hand. This part goes quick! It has to! The arm can only take so much! Here I am simply making several overlapping dents in the metal following the line of the client's scapula, steep towards the spine and feathering it out towards the arm's rolled edge.
A blacksmith of my acquaintance once watched me bouging a breastplate, and he made a comment that there were only three reasons why a blacksmith would go straight to hell. They are, according to him, "laming a horse", (with a bad shoe)," not charging enough for the job", and "pounding on cold steel". Well, I don't think my armour will cause a horse, or a client to go lame, and yeah, I probably undercharge for my work, and all my steel is hammered out cold. Guess I'll be hitting the "down" button when I punch the clock for the last time!!!
Back in the early days of this craft, there were silversmiths, goldsmiths, blacksmiths and whitesmiths. The blacksmith worked with hot metal....the oxides and fluxes he used makes the metal black as soot! Most iron work has a black coating on it even today! The whitesmith became the modern "panel basher", or auto body man. The armourer traditionally did his work cold, and only occasionally resting it in the fire to relieve its stress. And then, rather than trying to push it around while hot, the whitesmith often lets it cool slowly in a cushion of ashes so that it has no hardness in it at all. That slow cooling is called "annealing". A backplate like this can only be done cold. The stresses you produce at this stage combine to create the magic of a well fitted back plate. Hot work would spoil the project.
Dishing or raising.....two different processes to describe a superficially similar result. A backplate must be dished down into a block of wood to work. You cannot raise a backplate by pounding the metal over a raising stake. Dishing stresses the metal a lot less than raising. Armourers will argue this point all day, however today I am showing the dishing operation that works so well and is so easy to do. The whole raising technique is for another day.
The pictures show how I follow the line of the shoulder blades. (The top picture shows what we want to do....the second and third show the sequence) Not only does this make room for the shoulders, but also causes the top of the armour to roll inwards, towards the back of the neck. I discovered this technique when I had the honour of cleaning a back plate for the Palace Museum in Malta.....the size, shape and orientation of the hammer marks on the inside clearly showed to me that this was the way to do it. Imagine my surprise and delight that when I bouged the shoulder blades exactly like that 16th century Milanese craftsman the metal "snapped" into perfect curves!
2 comments:
You are a true craftsman. I am very intrigued by this whole process and found these posts really interesting. and that surprised me.
You are so kind. I am trying to make a potentially boring subject...metal bashing... interesting. Its not the bashing out of the steel, but rather the thought that goes into it which is interesting. When I do a demo at a county fair, I cannot say all the stuff about the kind of wood you use, or polish the hammers. This may become a manual of armour making, or possibly just a chance to order my thoughts. If you think there are paragraphs in this rambling narrative which are not necessary, or should be re-ordered, speak up!
Eventually I shall simply put this up on my web site. Not quite sure where though....its a big web site, and this might make it even more unmanagable than it is now! grin!
Post a Comment